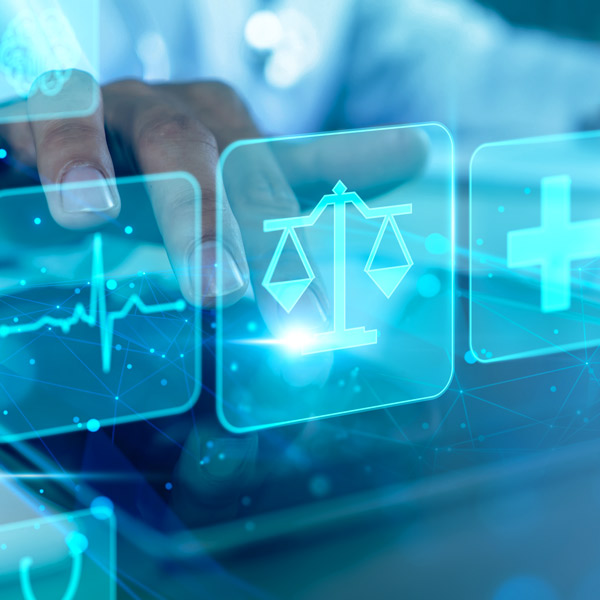
QUICK ACCESS TO OUR SERVICE PAGES
Product Development
Product Design
Prototype Development
Pre-Manufacturing
Design for Manufacturing (DFM)
Manufacturing Documentation
Pilot Production
Regulatory Compliance
Manufacturing
Supply Chain Management
Product Assembly
Product Testing & Calibration
Post-Manufacturing
Product Delivery
Product Support
Sustaining Engineering
Planning a Project?
Let's see if there is a fit
Product Resources collaborates on the design and manufacturing of a robot-assisted surgical device.
Background
Product Resources has significant experience designing and building computer-based instrumentation for the pharmaceutical and life sciences industries.
We had been working under our ISO 9001 certification since the mid-1990’s, but in 2012 we added ISO 13485 to allow us to manufacture medical devices using a recognized quality standard.
This additional level of control is necessary considering the seriousness of medical devices and the risks that they can pose to patients and users.
The new certification has allowed Product Resources to enter new markets while leveraging our expertise in computer control equipment and instrumentation.
The Challenge
In 2020, we were approached by a major manufacturer of medical equipment that needed a quick turnaround on the design and prototype of an enclosure for the computer control unit of a new surgical device.
The system was in the alpha prototype stage and needed design engineering and quick-turn manufacturing of prototypes for the customer’s testing.
The surgical device was a breakthrough robotic-assisted medical device with many components and sub-assemblies.
This initial project has evolved into an ongoing relationship involving a series of similar projects for the same end-product.
Project 1
This initial assignment called for the design of a sheet metal enclosure and bracketry for a control unit for a robotic-assisted surgical device. The design required the mounting of multiple computers, custom electronics, and peripheral devices.
Based on our progress and suggestions, this quickly grew to include the design of the cooling system and the cable management within the enclosure.
We were responsible for completing the design based on the design requirements and building 5 prototypes that incorporated a set of custom cables for Beta testing of the system at our customers engineering facility.
We were then tasked with designing the manufacturing process, PFMEA, and writing validation protocols for the manufacturing process.
Project 2
This second assignment followed the same pattern as the first assignment except that involved creating an enclosure and electrical design for a system to drive a remote “satellite” video console and power distribution for the same larger end-product.
We were given the product requirements and a mechanical mockup of the desired system.
We then developed a design for the enclosure and electronics, followed by the manufacturing process, PFMEA, and validation protocols.
Project 3
The third project for this system required us to manufacture a pilot production run and execute the validation protocol for both the main console (project 1) and the satellite console (project 2).
This process included:
- Verifying the supply chain organization and risk assessment was complete.
- Verifying the process flow for each component was properly documented and executed.
- Verifying the sub-assembly processes were documented and executed as intended.
- Verifying the test procedures properly captured the operation of the system and were sensitive to the identified failure modes.
- Verifying that the packaging for the unit was adequate for shipment to various locations.
- Building a significant number of both the computer console and the satellite console.
Project 4
As is often the case, we were later asked to update the design of the computer console by incorporating some new features that had been recommended by customers.
This was a project with significant updates to the original product.
The project included the design of new hardware and cabling and prototyping for three units to be used for additional development and regulatory testing. We also were tasked with the manufacturing process modifications and FMEAs required as well as a validation of the modifications.
The power of being nimble
We were told from the beginning we were assigned this project because we had the ability to be nimble in our approach to design and manufacturing – as well as our ability to handle “change control” without missing a beat.
Of course, we had to meet all the necessary requirements as a qualified contract manufacturer, but we also had to meet some very difficult deadlines.
It was always the intent of the customer to transfer the manufacturing of the computer console and the satellite console to their manufacturing facility once there was a validated design and manufacturing process. In the end though, the customer decided it was better to leave the manufacturing of the product in our facility in Newburyport MA.
Learn more
Find out more about Product Resources and how our design, engineering and manufacturing services could fit into your product development process.
Call 978-524-8500.